The Scientific Research Behind Porosity: A Comprehensive Guide for Welders and Fabricators
Understanding the intricate mechanisms behind porosity in welding is vital for welders and makers aiming for remarkable craftsmanship. From the structure of the base materials to the complexities of the welding procedure itself, a multitude of variables conspire to either aggravate or ease the visibility of porosity.
Comprehending Porosity in Welding
FIRST SENTENCE:
Exam of porosity in welding exposes important insights into the integrity and top quality of the weld joint. Porosity, characterized by the visibility of cavities or spaces within the weld steel, is an usual worry in welding procedures. These gaps, otherwise appropriately addressed, can compromise the structural stability and mechanical residential or commercial properties of the weld, causing potential failings in the ended up item.
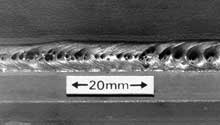
To spot and measure porosity, non-destructive testing approaches such as ultrasonic screening or X-ray assessment are often employed. These techniques enable for the identification of interior flaws without jeopardizing the honesty of the weld. By analyzing the size, shape, and distribution of porosity within a weld, welders can make informed decisions to improve their welding procedures and achieve sounder weld joints.

Variables Influencing Porosity Formation
The incident of porosity in welding is affected by a myriad of variables, ranging from gas protecting efficiency to the intricacies of welding parameter setups. Welding criteria, including voltage, existing, travel speed, and electrode kind, also influence porosity formation. The welding method used, such as gas metal arc welding (GMAW) or secured steel arc welding (SMAW), can influence porosity development due to variants in warm circulation and gas coverage - What is Porosity.
Impacts of Porosity on Weld Top Quality
Porosity development considerably endangers the structural honesty and mechanical buildings of welded joints. When porosity is present in a weld, it produces spaces or dental caries within the material, minimizing the overall stamina of the joint. These spaces function as stress focus factors, making the weld extra susceptible to splitting and failing under lots. The presence of porosity likewise damages the weld's resistance to corrosion, as the trapped air or gases within the spaces can react with the surrounding atmosphere, bring about destruction with time. Additionally, porosity can hinder the weld's capability to stand up to stress or effect, more threatening the total quality and integrity of the bonded framework. In critical applications such as aerospace, automobile, or structural constructions, where security and longevity are extremely important, the damaging impacts of porosity on weld quality can have severe effects, emphasizing the value of minimizing porosity with appropriate welding methods and treatments.
Strategies to Reduce Porosity
To enhance the top quality of welded joints and ensure structural stability, welders and fabricators utilize specific methods targeted at decreasing the development of gaps and dental caries within the material throughout the welding procedure. One effective technique to reduce porosity is to ensure appropriate product preparation. This consists of comprehensive cleansing of the base steel to get rid of any kind of contaminants such as oil, oil, or moisture that might add to porosity formation. Furthermore, utilizing the appropriate welding specifications, such as the proper voltage, current, and travel rate, is crucial in stopping porosity. Keeping a constant arc size and angle throughout welding also helps in reducing the likelihood of porosity.

Additionally, picking the right protecting gas and keeping correct i was reading this gas circulation prices are necessary in reducing porosity. Utilizing the suitable welding technique, such as back-stepping or employing a weaving movement, can likewise help distribute heat evenly and try this reduce the possibilities of porosity formation. Lastly, ensuring proper ventilation in the welding setting to get rid of any kind of prospective resources of contamination is important for accomplishing porosity-free welds. By executing these techniques, welders can effectively decrease porosity and generate high-grade bonded joints.
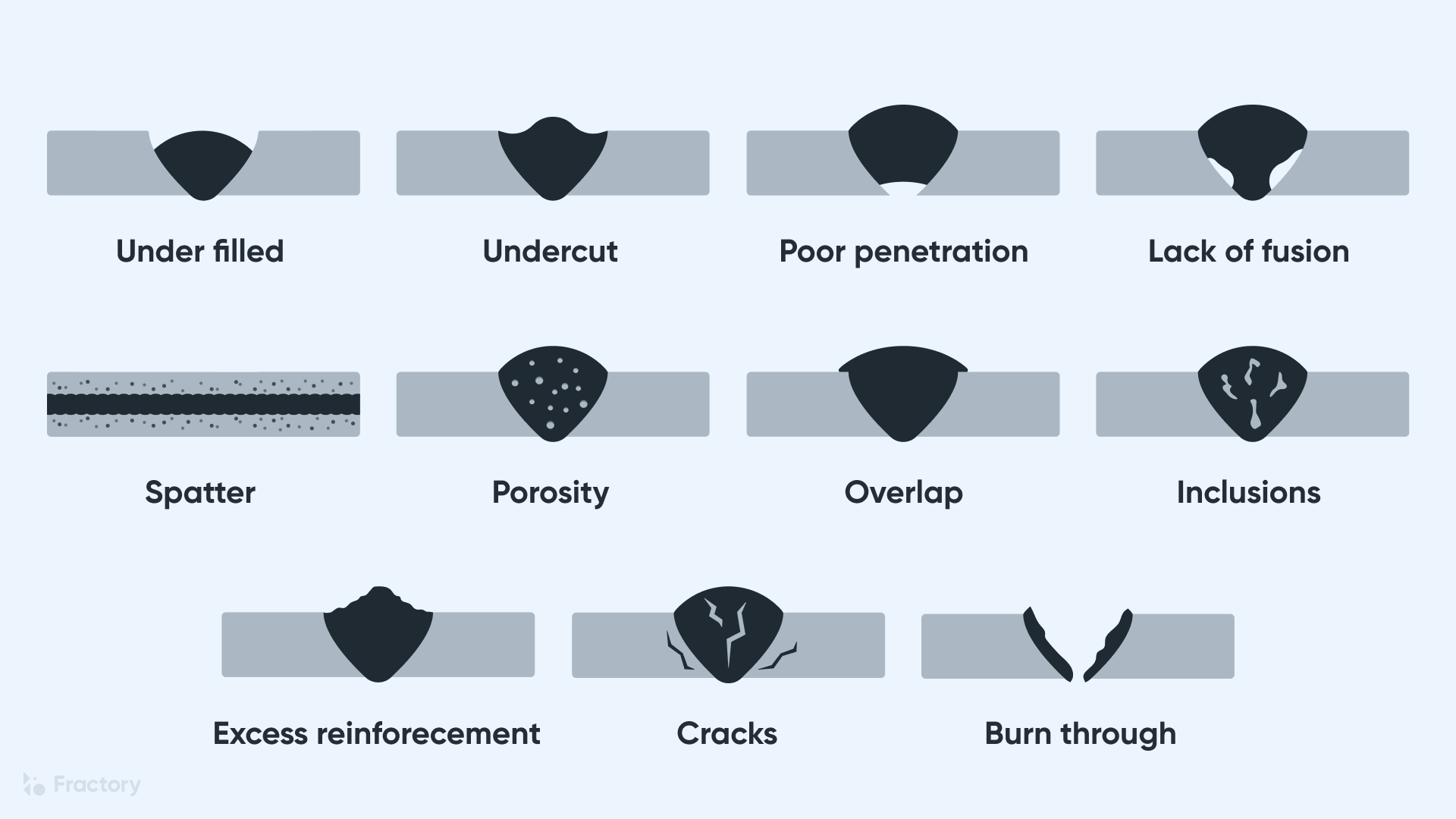
Advanced Solutions for Porosity Control
Carrying out advanced technologies and ingenious methods plays an essential role in attaining exceptional control over porosity in welding processes. One sophisticated solution is using innovative gas mixes. Securing gases like helium or a mixture of argon and hydrogen can help in reducing porosity by supplying better arc stability and enhanced gas insurance coverage. Furthermore, using sophisticated welding techniques such as pulsed MIG welding or changed atmosphere welding can likewise aid alleviate porosity issues.
An additional sophisticated remedy involves the usage of advanced welding devices. For example, using tools with integrated attributes like waveform control and advanced source of power can enhance weld quality and minimize porosity risks. The implementation of automated welding systems with precise control over parameters can considerably decrease porosity defects.
Furthermore, incorporating advanced surveillance and examination modern technologies such as real-time X-ray imaging or automated ultrasonic screening can assist in spotting porosity early in the welding process, allowing for immediate corrective activities. Generally, incorporating these sophisticated solutions can greatly boost porosity control and boost the general quality of bonded parts.
Final Thought
In final thought, understanding the scientific research behind porosity in welding is important for welders and makers to produce high-grade welds - What is Porosity. Advanced i loved this services for porosity control can better boost the welding process and make sure a solid and reputable weld.